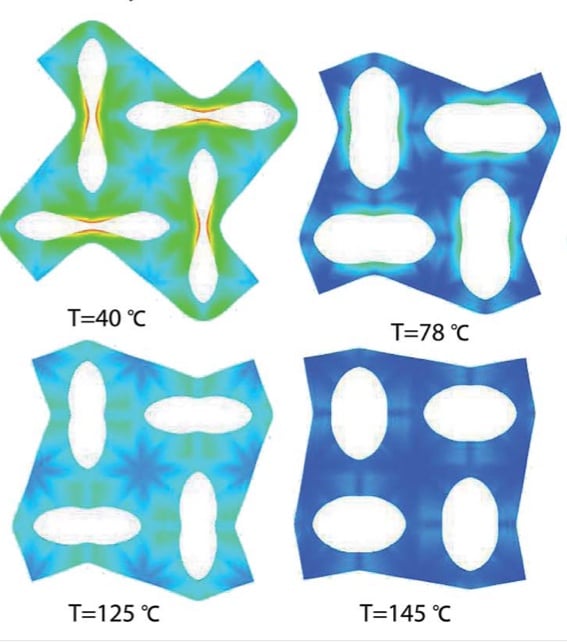
Shape-memory behavior in polymers describes the ability to store a programmed shape indefinitely and fully recover to an original shape in response to an environmental trigger. The materials are attractive for medical applications because they can be designed for biocompatibility, biodegradability, and controlled drug delivery. Moreover, they can store and recover large deformation, which is desirable for deployable and morphing structures (Perkins et al. 2004). For amorphous networks, shape-memory behavior is realized by programming around the glass transition temperature, Tg. In a typical shape-memory cycle, the material is heated above Tg, deformed to the desired shape, then cooled rapidly below the Tg to fix the programed shape for indefinite storage. The permanent shape can be recovered by heating the device to above the Tg or by immersing in solvent to depress the Tg.
The aims of this project is to investigate the effect of thermomechanical programming (deformation and temperature history), thermomechanical properties, and physical and environmental aging on the shape memory behavior under a variety of mechanical constraints. Our approach is to develop constitutive models that describe the key time-dependent mechanisms of the glass transition: (1) viscoelasticity, (2) structural relaxation, and (3) stress-activated viscous flow below Tg.
Figure 1: (a) Free recovery of a tert-butyl-acrylate SMP strip during heating immediately after shape programing and (b) after aging for 180 days comparing experiments and simulations. Finite element simulation of the free recovery of (c) a folded SMP stent and (d) of a constrained SMP film with an array of 4 holes showing a sequence of pattern transformations.
Figure 2: Finite element simulation of the recovery of SMP tube driven by water absorption at room temperature and
Collaborators
- Chris Yakacki, Ph.D. Assistant Professor, Department of Mechanical Engineering, University of Colorado Denver
- Carl Frick, Ph.D. Assistant Professor, Department of Mechanical Engineering, University of Wyoming
- David Safranski, Ph.D., Research Scientist, MedShape, Inc., Atlanta Georgia
- H. Jerry Qi, Ph.D. Professor, Department of Mechanical Engineering, Georgia Institute of Technology